2014年12月15日,工信部首發(fā)《全國工業(yè)能效指南》,對主要有色金屬產(chǎn)品和工序能效提出了明確要求?!吨改稀凡坏珜ζ髽I(yè)減少能耗具有重要指導(dǎo)意義,而且對行業(yè)和地方化解產(chǎn)能過剩、結(jié)構(gòu)調(diào)整、招商引資、完善布局等工作提供了可參考的“硬指標(biāo)”?!吨改稀钒ǎ含F(xiàn)有企業(yè)限定值、新進(jìn)企業(yè)準(zhǔn)人值、行業(yè)平均值、標(biāo)桿企業(yè)值參考值和國際先進(jìn)值等。表5-7~表5-11分別為氧化鋁、電解鋁、銅冶煉、鉛冶煉、鋅冶煉單位產(chǎn)品的綜合能耗。
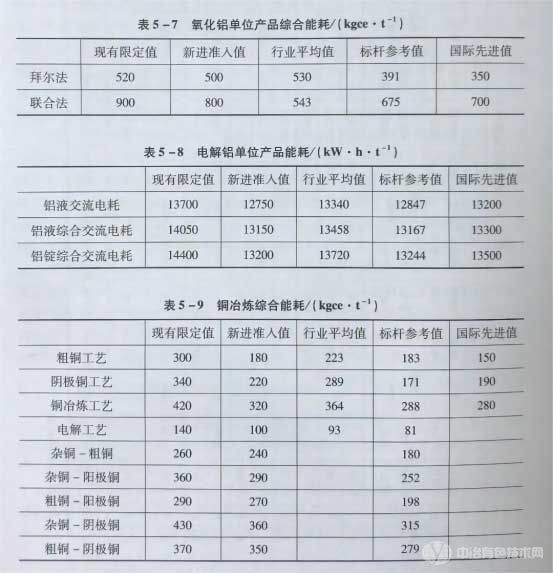
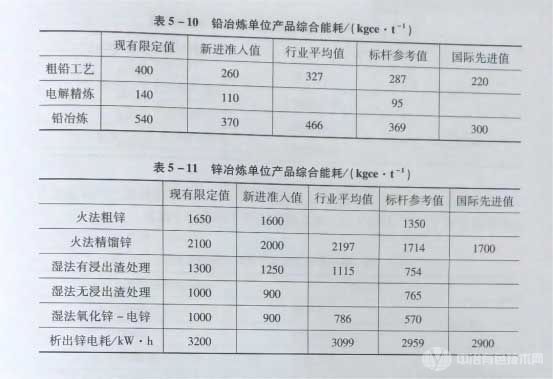
鋁冶金企業(yè)單位產(chǎn)品能源消耗
(1)氧化鋁企業(yè)單位產(chǎn)品能源消耗限額(GB 25327——2010)
現(xiàn)有氧化鋁企業(yè)單位產(chǎn)品能耗限額限定值見表5-12。表中指標(biāo)基于拜耳法礦石入磨鋁硅比大于8.5,其他工藝入磨鋁硅比大于7的條件下提出。
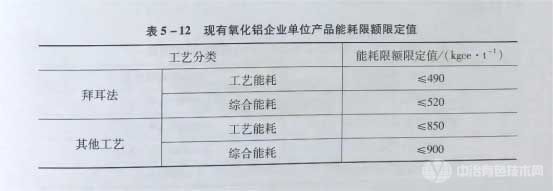
新建氧化鋁企業(yè)單位產(chǎn)品能耗限額準(zhǔn)人值見表5-13。表中指標(biāo)基于拜耳法礦石入磨鋁硅比大于8.2,其他工藝人磨鋁硅比大于7的條件下提出。
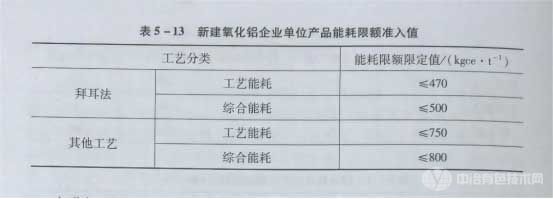
氧化鋁企業(yè)單位產(chǎn)品能耗限額先進(jìn)值見表5-14。表中指標(biāo)基于拜耳法礦石入磨鋁硅比大于8.5,其他工藝人磨鋁硅比大于7的條件下提出。
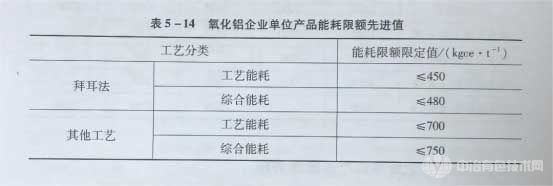
(2)電解鋁企業(yè)單位產(chǎn)品能源消耗限額(GB 21346—2013)
現(xiàn)有電解鋁企業(yè)單位產(chǎn)品能耗限額限定值、新建電解鋁企業(yè)單位產(chǎn)品能耗限額準(zhǔn)入值和電解鋁企業(yè)單位產(chǎn)品能耗限額先進(jìn)值分別如表5-15,表5-16和表5-17所示。
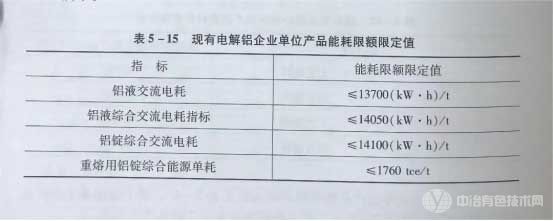
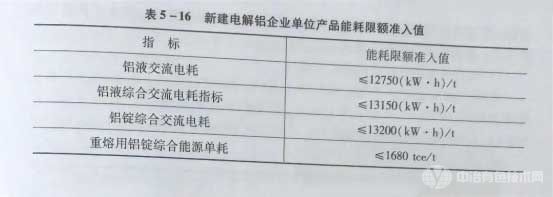

(3)我國氧化鋁生產(chǎn)的主體流程
圖5-2所示為我國各種氧化鋁生產(chǎn)技術(shù)的產(chǎn)量分布。與2005年之前相比,我國氧化鋁生產(chǎn)的主體技術(shù)結(jié)構(gòu)已經(jīng)發(fā)生了根本性的變化,節(jié)能的拜耳法已經(jīng)替代混聯(lián)法,成為我國氧化鋁生產(chǎn)的主體流程,拜耳法生產(chǎn)的氧化鋁已占我國總產(chǎn)量的86%左右。即使在鋁土礦品位較低的北方地區(qū),新建或擴(kuò)建的氧化鋁廠也均采用拜耳法或改進(jìn)的拜耳法。
改變主體生產(chǎn)流程的主要驅(qū)動力是節(jié)能。只有拜耳法才能保證氧化鋁生產(chǎn)的低能耗。主體流程的改變主要通過如下途徑實(shí)現(xiàn):部分關(guān)停高能耗的燒結(jié)法,或轉(zhuǎn)為生產(chǎn)化學(xué)品氧化鋁;混聯(lián)法逐漸向串聯(lián)法過渡,提高了拜耳法在聯(lián)合法中的
比例;新建的氧化鋁廠全部采用拜耳法;開發(fā)應(yīng)用處理中低品位鋁土礦的改進(jìn)型拜耳法:如選礦拜耳法和石灰拜耳法。
(4)國內(nèi)外氧化鋁生產(chǎn)的能耗比較
世界2010年氧化鋁平均能耗為14.5GJ/t,即495kgce/t。世界2011年氧化鋁平均能耗14 GJ/t,折合478 kgce/t。世界拜耳法平均能耗為11.2 GJ/t,即382kgce/t,其中低溫拜耳法溶出為8~11GJ/t;高溫拜耳法溶出為9~14GJ/t。
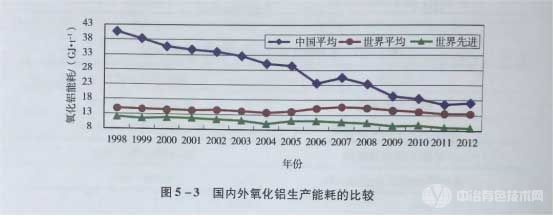
世界能耗最高的是以霞石為原料的阿欽斯克氧化鋁廠,高達(dá)57.89 GJ/t,即1978 kgce/t。世界上能耗最低的氧化鋁廠是巴西的阿魯諾特氧化鋁廠,能耗僅為8.37 GJ/t,即285 kgce/t。由圖5-3可見,南美洲氧化鋁企業(yè)的平均能耗達(dá)到了世界領(lǐng)先水平,目前已低于10 GJ/t,比世界平均能耗低約5 GJ/t。
我國氧化鋁能耗在過去的七年來持續(xù)快速下降(見圖5-4),累計降低幅度超過40%;2011年至2012年間達(dá)到17 GJ/t左右,明顯縮短了與國外的差距,已接近世界氧化鋁平均能耗。
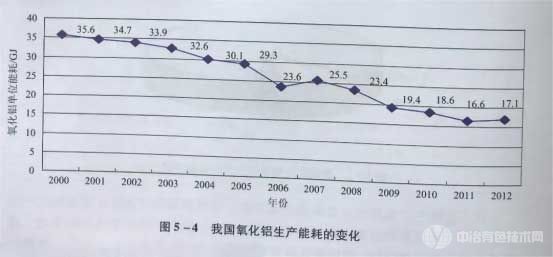
國內(nèi)外氧化鋁生產(chǎn)能耗差距的縮小主要依靠我國大力推廣應(yīng)用節(jié)能的拜耳法以及大規(guī)模開發(fā)應(yīng)用一系列重大節(jié)能關(guān)鍵技術(shù)和裝備。但同時也可以看出,仍有很大的節(jié)能潛力和空間。
(5)我國電解鋁的主體技術(shù)
圖5-5所示為我國現(xiàn)有鋁電解槽的電流強(qiáng)度分布比例。我國已基本淘汰160kA以下的自焙槽和小型預(yù)焙槽,大型預(yù)焙槽鋁電解技術(shù)已成為我國鋁電解的主體技術(shù),300 kA 以上的大型預(yù)焙槽技術(shù)在新建或擴(kuò)建的電解鋁廠得到了廣泛應(yīng)用。
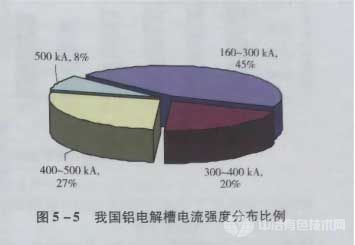
近年來所有新建的鋁電解廠普遍采用了大于400kA的大規(guī)模、大容量鋁電解技術(shù)。400kA以上的大型預(yù)焙槽生產(chǎn)線已建成近20條,數(shù)家500kA大型預(yù)焙槽生產(chǎn)線已建成投產(chǎn),600kA鋁電解槽技術(shù)已于2012年在中國鋁業(yè)連城分公司開始進(jìn)行工業(yè)試驗(yàn)。鋁電解槽預(yù)焙化、大型化、節(jié)能化和智能化已成為我國鋁電解產(chǎn)業(yè)技術(shù)的主要發(fā)展方向。
(6)國內(nèi)外電解鋁的能耗狀況
節(jié)能已成為世界鋁電解工業(yè)技術(shù)發(fā)展的主流。在世界原鋁工業(yè)的發(fā)展路線圖中,節(jié)能是鋁電解新技術(shù)開發(fā)的核心目標(biāo):以低能量輸入實(shí)現(xiàn)平均電流效率97%;通過技術(shù)改造實(shí)現(xiàn)能耗13kW·h/kg,遠(yuǎn)期以低成本方式實(shí)現(xiàn)能耗11kWh/kg,而且環(huán)境和社會可接受。
圖5-6、圖5-7為國內(nèi)外鋁電解企業(yè)平均能耗隨時間的變化情況。中國鋁電解平均能耗逐年以較快的速度下降,2012年平均綜合交流電耗已降低到13844 kW·h/t。
從2003年起我國鋁電解平均能耗就低于世界平均值。而世界上能耗較低的大洋洲(包括澳大利亞和新西蘭)的電解鋁企業(yè)的能耗卻仍然維持在14500~15000kWh/t的較高水平。
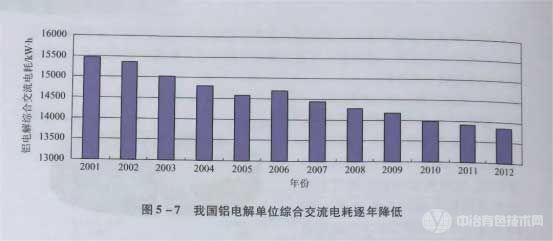
中國電解鋁近幾年大幅度的節(jié)能有力地推動了世界鋁電解平均能耗的降低。2011年中國鋁電解平均能耗已比世界平均能耗低800kW·h/t。由此可見,中國已經(jīng)成為世界鋁電解節(jié)能的主力軍,也是世界鋁電解能耗最低的原鋁生產(chǎn)國。