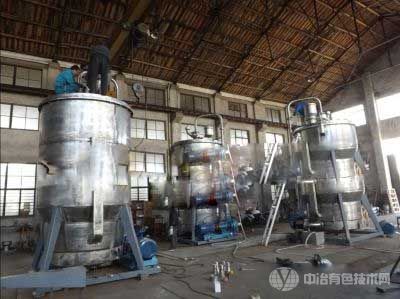
一、前言
近年來(lái)一種含有銅、鈷、鐵等多元素合金原料進(jìn)入國(guó)內(nèi)市場(chǎng)。該原料含銅70%以上,其它為鐵、鈷等。除去合金表面的氧化層后合金略顯紅色,俗稱紅合金。該合金如能用濕法處理應(yīng)當(dāng)是一種理想的處理工藝,因此能否經(jīng)濟(jì)合理地完成浸出工序就至關(guān)重要了。我所經(jīng)實(shí)驗(yàn)室小試后與華東某企業(yè)合作進(jìn)行了浸出中試,中試結(jié)果顯示:在稀硫酸介質(zhì)中以空氣作為氧化劑,使用微泡中和槽作浸出設(shè)備是一種較理想的技術(shù)方案。
二、原料狀況
紅合金原始狀態(tài)為黑色或棕黑色球狀顆粒,大顆粒直徑達(dá)5~8mm,粒度在4目到30目之間的約占90%,化學(xué)成份見(jiàn)表1。
紅合金化學(xué)成份 % 表1

三、浸出試驗(yàn)
(一) 實(shí)驗(yàn)室試驗(yàn)
筆者在實(shí)驗(yàn)室對(duì)紅合金采用了多種介質(zhì)不同條件的浸出探索。根據(jù)實(shí)驗(yàn)結(jié)果,考慮到后續(xù)工藝對(duì)浸出后液的要求及以微泡中和槽作浸出設(shè)備的要求等綜合因素得出下列結(jié)論:
1、 在稀硫酸介質(zhì)中,以空氣作為氧化劑,紅合金可以順利浸出,浸出率大于99.5%。
2、 浸出后液酸度可以控制在10~25g/l之間。
3、 浸出溫度75℃~85℃時(shí)有較快的浸出速度。
4、 浸出液過(guò)濾性能良好,濾渣為易懸浮固體,其主要成份為碳。
(二) 浸出反應(yīng)的機(jī)理
應(yīng)當(dāng)指出:在低酸度、空氣作氧化劑的條件下,不是所有的Cu、Co、Fe等多元合金都能順利浸出,因此實(shí)驗(yàn)室小試是非常必要的。本文中的紅合金小試結(jié)果是非常理想的,合金的溶解可能按下式進(jìn)行。
Me+?O2+H2SO4=Me2++SO42-+H2O- ……①
(Me=Cu、Fe、Co、Ni等)
Me+Cu2+=Cu+Me2+ ……②
(Me=Co、Fe、Ni等)
根據(jù)電化反應(yīng)數(shù)據(jù)②式反應(yīng)是很容易進(jìn)行的,因此紅合金的浸出速度實(shí)際取決于Cu的浸出速度。
Cu+?O2+H2SO4=Cu2++SO42-+H2O ……③
而能夠使式③反應(yīng)快速進(jìn)行正是微泡中和槽(原始設(shè)計(jì)為溶銅專用設(shè)備)的優(yōu)勢(shì)所在。
(三) 中試設(shè)備
中試采用WKR-0.5微泡中和槽見(jiàn)圖1,其有效反應(yīng)容積2m3,主材質(zhì)為Cr18Ni8不銹鋼,設(shè)備局部易磨損部位采用耐酸陶瓷和超高分子聚乙烯等材料。
微泡中和槽主要由反應(yīng)器、水-氣噴射器、液氣分離器(緩沖器)和循環(huán)泵等四大部件組成,其中水—?dú)鈬娚淦鞯奶厥庠O(shè)計(jì)能使空氣與浸出液乳化混合。當(dāng)乳化液通過(guò)固體物料時(shí)空氣以微氣泡方式與物料充分接觸,保證了較高的反應(yīng)界面,同時(shí)乳化液在上升過(guò)程中的強(qiáng)烈攪拌作用也有利于反應(yīng)物的擴(kuò)散,因此微泡中和槽在用于溶銅時(shí)具有較高的溶銅速度(12kg~50kg/m3·h)。值得指出的是由于溶銅反應(yīng)是放熱反應(yīng),反應(yīng)速度高時(shí)產(chǎn)生的熱量也會(huì)更多,加上微泡中和槽用于溶銅時(shí)氧的利用率可達(dá)30%~50%,這就避免了大量鼓風(fēng)所造成的熱量損失。實(shí)踐證明微泡中和槽作為溶銅設(shè)備時(shí)可以實(shí)現(xiàn)自熱運(yùn)行,甚至自熱起動(dòng),超溫時(shí)還必須采取降溫措施。
微泡中和槽按連續(xù)工作制設(shè)計(jì),設(shè)備還配有如下部件:
①.旋流式固液分離器——用于浸出后液排出前的固液分離,使隨溶液流動(dòng)的金屬小顆?;氐椒磻?yīng)器,使比重較輕的浸出殘?jiān)S浸出后液排出反應(yīng)器。
②酸霧冷凝器——回收反應(yīng)殘除氣體中的酸霧改善排放指標(biāo),同時(shí)利用低溫的浸出前液吸收煙氣中的部分熱量。
③液位控制器——設(shè)備采用底部溶液經(jīng)循環(huán)泵出口分流的方式排液。液位控制器能在補(bǔ)液速度變化時(shí)自行調(diào)整排液速度,保持反應(yīng)器內(nèi)的正常液位。
④排污口——微氣泡有強(qiáng)烈的氣浮作用,碳粉等雜質(zhì)會(huì)在反應(yīng)器液面逐步聚集,通過(guò)排污口排除雜質(zhì)也是維持設(shè)備連續(xù)運(yùn)行的重要部件。
(四) 中試工藝條件及概況
1、浸出工藝條件
物料:直接采用原始狀態(tài)的紅合金,不作粒度要求。
浸出前液:H2SO4160~210g/l;反應(yīng)溫度75℃~85℃;
補(bǔ)液速度:4~7l/min;浸出后液酸度:15~30g/l
2、中試概況
中試在2009年12月~2010年元月期間兩次開機(jī)運(yùn)行,前后運(yùn)行約15d。
因紅合金未作破碎處理粒度較大,中試時(shí)采用了(半固定床)強(qiáng)制堆浸的方式。首次投料約7t(第二次開機(jī)投料約3.5t),投料層高度達(dá)反應(yīng)器高度的1/3~2/3。注入浸出前液前首先注入適量清水(防止設(shè)備被腐蝕)開啟循環(huán)泵后逐步補(bǔ)加浸出前液,并維持反應(yīng)器內(nèi)酸度不超過(guò)30g/l。兩次開機(jī)均采用冷起動(dòng)經(jīng)6h左右自動(dòng)升溫到75℃以上,溫度超過(guò)85℃時(shí)偶爾開啟冷卻水降溫。浸出后液含Cu2+80~95g/l;Co2+7g/l左右H2SO4<30g/l。
中試出現(xiàn)下列問(wèn)題:
①WKR-0.5微泡中和槽由WR-0.5A原型調(diào)整設(shè)計(jì)后制成,在半固定床狀態(tài)下運(yùn)行時(shí)發(fā)現(xiàn)溶液循環(huán)通道設(shè)計(jì)不夠合理,因此循環(huán)泵運(yùn)行一直不穩(wěn)定,致使水—?dú)鈬娚淦魑肟諝饬棵黠@不足,甚至出現(xiàn)喘息狀況,這就直接造成了反應(yīng)攪拌強(qiáng)度不夠、氧化能力不足的問(wèn)題。
②反應(yīng)器部分構(gòu)件尺寸不合理,造成乳化液分布不均勻,“死角”部分出現(xiàn)碳粉和置換銅粉共同結(jié)塊現(xiàn)象,以致水、氣通道阻塞,反應(yīng)面積下降,結(jié)果形成浸出速度逐步下降的趨向。
③局部零件材質(zhì)不合格,出現(xiàn)腐蝕損壞,影響部件功能。
四、結(jié)論與展望
通過(guò)十多天的中試運(yùn)行,得出下述結(jié)論:
1、日平均浸出能力為460kg(設(shè)計(jì)標(biāo)準(zhǔn)應(yīng)>500kg);
2、噸合金浸出電耗約450kwh(設(shè)計(jì)標(biāo)準(zhǔn)應(yīng)為≤400kwh);
3、在設(shè)備存在部分問(wèn)題的條件下仍能實(shí)現(xiàn)自熱起動(dòng),自熱運(yùn)行。
4、紅合金在H2SO4介質(zhì)中低酸度氧化浸出工藝可行。
筆者認(rèn)為,中試暴露的問(wèn)題主要是設(shè)備局部設(shè)計(jì)的問(wèn)題,而改進(jìn)設(shè)計(jì)是比較容易的。筆者估計(jì)通過(guò)改進(jìn)后的WRT-型(通用型)微泡中和槽完全可以解決紅合金中試中出現(xiàn)的問(wèn)題,其生產(chǎn)能力、能耗等指標(biāo)將有大幅改善。WRT-型通用微泡中和槽有望成為能以固定床、半固定床、流化床等多種狀態(tài)工作的一種高效多相浸出設(shè)備。