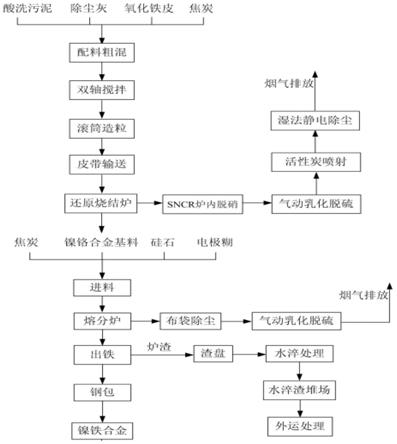
1.本發(fā)明涉及不銹鋼酸洗污泥回收技術(shù)領(lǐng)域,具體領(lǐng)域?yàn)椴讳P鋼酸洗污泥資源回收利用方法。
背景技術(shù):
2.不銹鋼企業(yè)在生產(chǎn)過(guò)程中,有大量不銹鋼酸洗污泥產(chǎn)生,不銹鋼酸洗污泥中含有 ni、cr、fe 等有價(jià)金屬元素,以及 caf2、mgo、sio2、caso4 等物質(zhì)。已被國(guó)家列入危險(xiǎn)廢物名錄,近年來(lái)隨著我國(guó)不銹鋼產(chǎn)量逐年增加,酸洗不銹鋼酸洗污泥的產(chǎn)生量也隨之增加。
3.隨著資源的日益枯竭和環(huán)保要求的不斷提高,不銹鋼企業(yè)在環(huán)境保護(hù)、資源利用方面臨嚴(yán)峻的挑戰(zhàn),如何合理利用這些酸洗不銹鋼酸洗污泥已成為全社會(huì)廣泛關(guān)注的焦點(diǎn),也關(guān)系到我國(guó)不銹鋼企業(yè)的健康發(fā)展。
4.如今國(guó)內(nèi)外對(duì)于不銹鋼酸洗污泥的處理與利用,無(wú)論利用制作建材還是回收其中的金屬元素或者是防滲填埋處理,都存在不足之處:一、濕法回收工藝比較復(fù)雜、不易操作,處理成本高昂,浸出液用量很大,不適合大規(guī)模工業(yè)化生產(chǎn);二、利用不銹鋼酸洗污泥制磚時(shí),在高溫焙燒過(guò)程中可能會(huì)使cr3+再次氧化為 cr6+,存在二次污染的問(wèn)題;三、對(duì)不銹鋼酸洗污泥的資源化利用大都涉及異地處理,在運(yùn)輸、堆存過(guò)程會(huì)產(chǎn)生二次污染;四、由于不銹鋼酸洗污泥中有價(jià)重金屬毒性較強(qiáng),并能長(zhǎng)期穩(wěn)定存在,如果采用防滲填埋的方式進(jìn)行處理,該處理方式不能徹底消除鎳、鉻、鋅等重金屬對(duì)環(huán)境和人類健康的影響,容易對(duì)地下水、生態(tài)環(huán)境造成二次污染,并且在外界環(huán)境的作用下有可能轉(zhuǎn)化為毒性更強(qiáng)的化合物,通過(guò)食物鏈等方式,使鎳、鉻、鋅等重金屬進(jìn)入人體,造成不同程度的中毒現(xiàn)象,最終危害人類健康,且該方式占用寶貴的土地資源導(dǎo)致資源成本增加,同時(shí)也造成鎳、鉻、鋅等資源的浪費(fèi)。
技術(shù)實(shí)現(xiàn)要素:
5.針對(duì)現(xiàn)有技術(shù)存在的不足,本發(fā)明的目的在于提供一種不銹鋼酸洗污泥資源回收利用方法。
6.為實(shí)現(xiàn)上述目的,本發(fā)明提供如下技術(shù)方案:一種不銹鋼酸洗污泥資源回收利用方法,其步驟為:(1)制球:將酸洗不銹鋼酸洗污泥、煉鋼除塵灰和氧化鐵皮混合制成球狀體;(2)燒結(jié)預(yù)還原:將球狀體進(jìn)行烘干、燒結(jié)、預(yù)還原后形成基料;(3)熔分冶煉:將預(yù)還原后的基料送入熔分爐內(nèi)還原冶煉形成液態(tài)鎳鉻合金和爐渣,并通過(guò)渣鐵分離得到相互分離的鎳鉻合金和爐渣;(4)煙氣處理:基料在熔分爐內(nèi)熔分冶煉過(guò)程中進(jìn)行除塵、脫硝、脫硫工藝對(duì)煙氣
進(jìn)行處理。
7.優(yōu)選的,步驟(1)的具體步驟為:將含水率 50 至 55%的酸洗不銹鋼酸洗污泥在混料場(chǎng)混入 6-8%的焦粉、 10%的煉鋼除塵灰、5%的氧化鐵皮,將混合完成后的原料通過(guò)傳送帶輸送方式進(jìn)入制球機(jī),同時(shí)啟動(dòng)制球機(jī),制球機(jī)不斷旋轉(zhuǎn),經(jīng)過(guò)20-40 分鐘運(yùn)行,原料形成直徑為 3-5cm 的球狀固體,從制球機(jī)的出料口出料。
8.優(yōu)選的,步驟(2)的具體步驟包括:
①
進(jìn)料:將制球機(jī)制得的球狀固體經(jīng)
皮帶輸送機(jī)輸送至還原爐爐頂后,自行滑落至旋轉(zhuǎn)布料器內(nèi),經(jīng)旋轉(zhuǎn)布料器在爐內(nèi)均勻布料;
②
烘干、燒結(jié)、預(yù)還原:首先在還原爐的干餾層利用爐內(nèi)高溫去除球狀固體中原料含有的水份,然后進(jìn)入爐膛后,原料中的焦炭粉和經(jīng)
鼓風(fēng)機(jī)吹入爐膛內(nèi)的空氣進(jìn)行劇烈燃燒,散發(fā)熱量,使還原層的溫度達(dá)到800-1200度,原料中的鐵、鎳、鉻元素在高溫下預(yù)還原結(jié)晶,生成基料。
9.③
出料:預(yù)還原后的基料經(jīng)鼓風(fēng)機(jī)吹入常溫空氣進(jìn)行冷卻,當(dāng)基料溫度降至80-120度后,由旋轉(zhuǎn)出料器排出爐膛,通過(guò)出料皮帶輸送機(jī)運(yùn)送至基料中轉(zhuǎn)庫(kù);
④
還原燒結(jié)爐采用分批進(jìn)料方式,每20至30min進(jìn)一次料,一批料為4噸,出料采用連續(xù)出料方式,出料速度140至150千克/分鐘,燒結(jié)產(chǎn)生的基料通過(guò)皮帶機(jī)送入中轉(zhuǎn)庫(kù)。
10.優(yōu)選的,步驟(3)的具體步驟包括:
①
、進(jìn)料:將鎳鉻合金基料、焦碳、硅石按每個(gè)批次2000kg:300kg:30kg的比例配比混合均勻后,投入熔分爐電極周圍;
②
、熔分爐冶煉:對(duì)熔分爐內(nèi)進(jìn)行升溫,熔分爐內(nèi)高溫條件下,以碳作為還原劑對(duì)基料進(jìn)行還原反應(yīng)得到鎳鉻合金和爐渣;
③
、出料:熔分爐出鐵時(shí)間為4小時(shí)一次,鎳鉻合金與爐渣同時(shí)從出鐵口放出,即生產(chǎn)出fe含量40至60%左右,鎳含量4至8%、鉻含量12至18%左右的鎳鉻合金,爐渣通過(guò)位于熔分爐一端兩個(gè)排渣口之中的一個(gè)排渣口排渣,爐渣通過(guò)流槽進(jìn)入渣池。
11.優(yōu)選的,步驟(4)中的脫硝工藝為采用sncr脫硝工藝,其具體步驟為:將含有nhx基的還原劑與水混合后,還原劑稀釋為10%濃度的溶液,通過(guò)噴槍將稀釋后的溶液噴入爐膛內(nèi),使得稀釋后的溶液與煙氣進(jìn)行sncr反應(yīng)生成氮?dú)夂退?br>
12.優(yōu)選的,步驟(4)中的脫硫工藝為采用氣動(dòng)乳化脫硫工藝,其具體步驟為:采用工業(yè)純堿、石灰作為脫硫劑,把工業(yè)純堿、石灰制成脫硫液,將煙氣在脫硫液中充分接觸傳質(zhì),將煙氣中的二氧化硫去除;脫硫后的煙氣經(jīng)除霧器除去細(xì)小液滴,然后排入有防腐層的濕煙囪,脫硫石膏漿經(jīng)脫水裝置脫水后運(yùn)出廠外處理。
13.與現(xiàn)有技術(shù)相比,本發(fā)明的有益效果是:一、資源及能源利用指標(biāo):本技術(shù)采用了多種節(jié)能設(shè)計(jì)及裝備,最大幅度的降低項(xiàng)目資源及能源利用指標(biāo),主要體現(xiàn)如下:1、本項(xiàng)目將不銹鋼酸洗污泥進(jìn)行就地處理利用,可解決對(duì)不銹鋼酸洗污泥的資源化利用大都涉及異地處理,在運(yùn)輸,重新放置過(guò)程會(huì)產(chǎn)生二次污染和高額運(yùn)輸、處理成本的問(wèn)題,具有可觀的經(jīng)濟(jì)環(huán)保效益;2、本項(xiàng)目生產(chǎn)工藝可以將不銹鋼酸洗污泥中的有價(jià)金屬元素和氟化鈣、氧化鈣等作為冶金輔料的物質(zhì)全部利用,不僅會(huì)產(chǎn)生較大的效益并
且會(huì)為環(huán)境保護(hù)和可持續(xù)發(fā)展做出巨大貢獻(xiàn);3、設(shè)備選型充分考慮了能效比、能效等級(jí)等參數(shù),兼顧了節(jié)能和環(huán)境保護(hù),清潔生產(chǎn)程度高。選擇符合能耗標(biāo)準(zhǔn)的水泵、電機(jī)、變壓器等,并采用的了就地補(bǔ)償、變頻器、plc控制、伺服電機(jī)等節(jié)電措施,有效降低產(chǎn)品能耗。對(duì)大于7.5kw的變負(fù)荷設(shè)備配套電機(jī)均加裝變頻控制,節(jié)電率超過(guò)10%;4、成品1530℃的鎳鉻合金基料熱料直接紅送至不銹鋼生產(chǎn)電爐直接用于生產(chǎn)(溫度約1200℃),減少了后續(xù)不銹鋼生產(chǎn)加熱所需的能耗,該技術(shù)是不銹鋼酸洗污泥經(jīng)高溫固化后直接在熔分爐內(nèi)進(jìn)行冶煉鎳鉻合金,作不銹鋼冶煉鎳鉻原料,可實(shí)現(xiàn)變廢為寶,達(dá)到減量化、無(wú)害化,節(jié)能減排,使不銹鋼酸洗污泥資源化高效利用,符合國(guó)家發(fā)展循環(huán)、綠色經(jīng)濟(jì)的產(chǎn)業(yè)政策。
14.二、產(chǎn)品指標(biāo):本技術(shù)最終產(chǎn)品為從酸洗不銹鋼酸洗污泥、氧化鐵皮、除塵飛灰中提煉生成的鎳鉻合金,其中原料中鎳、鉻等有用金屬元素回收率90%以上,生產(chǎn)的鎳鉻合金原料中含鎳4-8%、含鉻12-18%左右,可直接送不銹鋼生產(chǎn)電爐或aod爐生產(chǎn)不銹鋼,均可滿足電爐或aod爐進(jìn)料要求。
15.三、廢物回收利用指標(biāo):本技術(shù)作為
固廢綜合利用改造提升項(xiàng)目,是固廢資源的“減量化、資源化、無(wú)害化”過(guò)程,本身就具有較高的環(huán)境效益和經(jīng)濟(jì)效益。本項(xiàng)目過(guò)程中仍會(huì)產(chǎn)生固體廢棄物,主要如下:一、熔分爐爐渣,爐渣經(jīng)相關(guān)資質(zhì)單位鑒定確定屬于一般固體廢物,主要成分是鈣和硅,銷售到水泥廠生產(chǎn)水泥。二、熔煉等過(guò)程布袋除塵系統(tǒng)產(chǎn)生的煉鋼除塵灰,該煉鋼除塵灰主要成分是鋅,可以作為鋅回收行業(yè)的原料進(jìn)行處置。本技術(shù)各類固廢的處置均滿足國(guó)家相應(yīng)的標(biāo)準(zhǔn)和規(guī)范要求,各類固廢均能做到100%安全處置。
附圖說(shuō)明
16.圖1為本發(fā)明的工藝流程圖。
具體實(shí)施方式
17.下面將結(jié)合本發(fā)明實(shí)施例中的附圖,對(duì)本發(fā)明實(shí)施例中的技術(shù)方案進(jìn)行清楚、完整地描述,顯然,所描述的實(shí)施例僅僅是本發(fā)明一部分實(shí)施例,而不是全部的實(shí)施例?;诒景l(fā)明中的實(shí)施例,本領(lǐng)域普通技術(shù)人員在沒(méi)有做出創(chuàng)造性勞動(dòng)前提下所獲得的所有其他實(shí)施例,都屬于本發(fā)明保護(hù)的范圍。
18.酸洗不銹鋼酸洗污泥中含有大量的鉻、鎳、鐵等金屬元素和氟化鈣、氧化鈣等物質(zhì),將酸洗不銹鋼酸洗污泥作為一種廉價(jià)的二次可再生資源,其中鉻、鎳、鐵等金屬元素可綜合回收并利用,同時(shí)酸洗不銹鋼酸洗污泥中的 caf2 可以作為冶金各個(gè)生產(chǎn)環(huán)節(jié)的熔劑或配料用于燒結(jié)配料、高爐熔劑、轉(zhuǎn)爐輔助材料、精煉爐造渣材料,甚至可以作為連鑄保護(hù)渣的成分利用。在不銹鋼企業(yè)就地將酸洗不銹鋼酸洗污泥中鉻、鎳、鐵等金屬元素和氟化鈣、氧化鈣等作為冶金輔料進(jìn)行綜合利用,不僅會(huì)產(chǎn)生較大的效益并且會(huì)為環(huán)境保護(hù)和可持續(xù)發(fā)展做出巨大貢獻(xiàn)。
19.請(qǐng)參閱圖1,采用還原爐燒結(jié)固化-熔分爐冶煉處理技術(shù),將不銹鋼酸洗污泥及其他配料經(jīng)高溫預(yù)還原后在熔分爐內(nèi)進(jìn)行冶煉生產(chǎn)鎳鉻合金,鎳鉻合金又作為不銹鋼生產(chǎn)的原料循環(huán)利用,從而最終達(dá)到不銹鋼酸洗污泥“減量化、無(wú)害化、資源循環(huán)利用”的目的,該
工藝主要原理是在高溫條件下,以焦炭作為還原劑,將不銹鋼酸洗污泥、煉鋼除塵灰及氧化鐵皮中的金屬氧化物還原。
20.不銹鋼酸洗污泥中的金屬元素以氫氧化物的形式存在,主要有ni(oh)2、fe(oh)2、mn(oh)2、cr(oh)3、cr(oh)6等,煉鋼除塵灰、氧化鐵皮中的金屬元素以氧化物的形式存在。在還原燒結(jié)爐中,不銹鋼酸洗污泥首先脫水,發(fā)生如下反應(yīng):(1)ni(oh)2→
nio+h2o
↑
(2)fe(oh)2→
feo+h2o
↑
(3)mn(oh)2→
mno+h2o
↑
(4)2cr(oh)3→
cr2o3+3h2o
↑
(5)cr(oh)6→
cro3+3h2o
↑
烘干脫水后的不銹鋼酸洗污泥中主要成分為nio、feo、mno等金屬氧化物,此時(shí)以焦炭作為還原劑,將不銹鋼酸洗污泥、煉鋼除塵灰、氧化鐵皮中的金屬氧化物進(jìn)行還原。各金屬氧化物還原反應(yīng)式為:(1)nio+c
→
ni+co
↑
(2)feo+c
→
fe+co
↑
(3)mno+c
→
mn+co
↑
(4)cr2o3+3c
→
2cr+3co
↑
(5)cro3+3c
→
cr+3co
↑
由于還原燒結(jié)爐內(nèi)的溫度一般為800-1200℃左右,在此溫度下不銹鋼酸洗污泥、煉鋼除塵灰、氧化鐵皮中的金屬氧化物無(wú)法完全被還原,且渣鐵無(wú)法實(shí)現(xiàn)分離,因此從燒結(jié)爐出來(lái)的燒結(jié)料送入熔分爐內(nèi)進(jìn)一步還原,熔分爐的溫度一般可以達(dá)到1400-1500℃,最高可達(dá)1900℃,在此溫度下99%以上的金屬氧化物可以被還原成金屬,在出鐵口實(shí)現(xiàn)渣鐵分離后,得到最終產(chǎn)品鎳鉻合金。
21.本發(fā)明提供一種技術(shù)方案:一種不銹鋼酸洗污泥資源回收利用方法,其步驟為:(1)制球:將不銹鋼酸洗污泥(
危廢,危廢代碼:336-064-17)、煉鋼除塵灰(危廢,危廢代碼:314-002-21)和煉鋼氧化鐵皮混合制成球狀體;(2)燒結(jié)預(yù)還原:將球狀體進(jìn)行烘干、燒結(jié)、預(yù)還原后形成基料;(3)熔分冶煉:將預(yù)還原后的基料送入熔分爐內(nèi)還原冶煉形成液態(tài)鎳鉻合金和爐渣,并通過(guò)渣鐵分離得到相互分離的鎳鉻合金和爐渣;(4)煙氣處理:基料在熔分爐內(nèi)熔分冶煉過(guò)程中進(jìn)行除塵、脫硝、脫硫工藝對(duì)煙氣進(jìn)行處理。
22.步驟(1)的具體步驟為:將含水率 50 至 55%的酸洗不銹鋼酸洗污泥在混料場(chǎng)混入 6-8%的焦粉、 10%的煉鋼除塵灰、5%的氧化鐵皮,將混合完成后的原料通過(guò)傳送帶輸送方式進(jìn)入制球機(jī),同時(shí)啟動(dòng)制球機(jī),制球機(jī)不斷旋轉(zhuǎn),經(jīng)過(guò)20-40 分鐘運(yùn)行,原料形成直徑為 3-5cm 的球狀固體,從制球機(jī)的出料口出料。
23.步驟(2)的具體步驟包括:
①
進(jìn)料:將制球機(jī)制得的球狀固體經(jīng)皮帶輸送機(jī)輸送至還原爐爐頂后,自行滑落至旋轉(zhuǎn)布料器內(nèi),經(jīng)旋轉(zhuǎn)布料器在爐內(nèi)均勻布料;
②
烘干、燒結(jié)、預(yù)還原:首先在還原爐的干餾層利用爐內(nèi)高溫去除球狀固體中原料
含有的水份,然后進(jìn)入爐膛后,原料中的焦炭粉和經(jīng)鼓風(fēng)機(jī)吹入爐膛內(nèi)的空氣進(jìn)行劇烈燃燒,散發(fā)熱量,使還原層的溫度達(dá)到8000-1200度,原料中的鐵、鎳、鉻元素在高溫下預(yù)還原結(jié)晶,生成基料。
24.③
出料:預(yù)還原后的基料經(jīng)鼓風(fēng)機(jī)吹入常溫空氣進(jìn)行冷卻,當(dāng)基料溫度降至80-120度后具體為100度左右,由旋轉(zhuǎn)出料器排出爐膛,通過(guò)出料皮帶輸送機(jī)運(yùn)送至基料中轉(zhuǎn)庫(kù);
④
還原燒結(jié)爐采用分批進(jìn)料方式,每20至30min進(jìn)一次料,一批料為4噸,出料采用連續(xù)出料方式,出料速度140至150千克/分鐘,燒結(jié)產(chǎn)生的基料通過(guò)皮帶機(jī)送入中轉(zhuǎn)庫(kù)。
25.步驟(3)的具體步驟為:熔分爐冶煉是將還原爐產(chǎn)生的基料配以一定量的焦炭、硅石、電極糊后,進(jìn)入熔分爐內(nèi),經(jīng)過(guò) 4 小時(shí)的高溫(1373-1523 度)還原冶煉, 形成液態(tài)鎳鉻合金和爐渣,最后通過(guò)渣鐵分離,得到最終產(chǎn)品鎳鉻合金的過(guò)程。 其詳細(xì)工藝過(guò)程如下:
①
、進(jìn)料:將鎳鉻合金基料、焦碳、硅石按每個(gè)批次2000kg:300kg:30kg的比例配比混合均勻后,投入熔分爐電極周圍,爐內(nèi)原料呈大錐體;
②
、熔分爐冶煉:對(duì)熔分爐內(nèi)進(jìn)行升溫,熔分爐內(nèi)高溫條件下,以碳作為還原劑對(duì)基料進(jìn)行還原反應(yīng)得到鎳鉻合金和爐渣,熔分爐內(nèi)所發(fā)生的化學(xué)反應(yīng)生產(chǎn)鎳鉻合金的主要過(guò)程是:碳還原氧化鉻生成 cr3c2,開(kāi)始還原溫度為 1385 度,生成鉻的反應(yīng)開(kāi)始溫度為 1520 度。在碳還原鉻料時(shí)得到的是含碳較高的鉻的碳化物,即鎳鉻合金。 熔分爐內(nèi)高溫條件下,以碳作為還原劑對(duì)基料中的 nio 及其他氧化物 (如 feo 等)進(jìn)行還原而得。還原過(guò)程中發(fā)生以下化學(xué)反應(yīng):nio+c
→?
ni+co
↑?
(t ≈420℃),feo+c
→
fe+co
↑
(t ≈650℃);
③
、出料:熔分爐出鐵時(shí)間為4小時(shí)一次,鎳鉻合金與爐渣同時(shí)從出鐵口放出,即生產(chǎn)出fe含量40至60%左右,鎳含量4至8%、鉻含量12至18%左右的鎳鉻合金,每批配料可生產(chǎn)約 1000kg 鎳鉻合金(根據(jù)進(jìn)料不同略有偏差)。鎳鉻合金鐵水經(jīng)扒渣后直接紅送至不銹鋼電爐進(jìn)行不銹鋼冶煉。出料后熔分爐內(nèi)料面會(huì)持續(xù)性下降,通過(guò)及時(shí)補(bǔ)充加料,以保持爐內(nèi)一定的料面高度。 熔分爐爐渣通過(guò)位于熔分爐一端兩個(gè)排渣口之中的一個(gè)排渣口排渣,爐渣溫度為 1450℃~1550℃,爐渣通過(guò)溜槽進(jìn)入水淬池。
26.步驟(4)中的脫硝工藝為采用sncr脫硝工藝,其具體步驟為:將含有nhx基的還原劑與水混合后,還原劑稀釋為10%濃度的溶液,通過(guò)噴槍將稀釋后的溶液噴入爐膛內(nèi),使得稀釋后的溶液與煙氣進(jìn)行sncr反應(yīng)生成氮?dú)夂退?br>
27.脫硝:脫硝采用sncr脫硝工藝,把含有nhx基的還原劑(本項(xiàng)目采用40%尿素溶液),經(jīng)輸送泵送至計(jì)量分配模塊,與稀釋水模塊送過(guò)來(lái)的水混合,尿素溶液被稀釋至10%,通過(guò)計(jì)量分配裝置精確分配到每個(gè)噴槍,然后經(jīng)過(guò)噴槍噴入爐膛,反應(yīng)區(qū)窗口溫度為800~1100℃,隨后尿素與煙氣中的nox進(jìn)行sncr反應(yīng)而生成n2和h2o。其反應(yīng)原理如下:co(nh2)2+2no
→
2n2+co2+2h2oco(nh2)2+h2o—》2nh3+co24no+4nh3+o2—》4n2+6h2o2no+4nh3+2o2—》3n2+6h2o6no2+8nh3—》7n2+12h2o
步驟(4)中的除塵工藝為采用旋風(fēng)除塵、布袋除、塵濕電除塵工藝,具體如下:
①?
、還原爐煙氣除塵:步驟一:旋風(fēng)除塵,還原爐產(chǎn)生煙氣流進(jìn)入旋風(fēng)
除塵器后,氣流在除塵器內(nèi)作旋轉(zhuǎn)運(yùn)動(dòng),氣流中的塵粒在離心力作用下向除塵器外壁移動(dòng),到達(dá)壁面,并在氣流和重力作用下沿壁面落入灰斗而達(dá)到分離的目的。煙氣進(jìn)入布袋除塵器步驟二:經(jīng)過(guò)旋風(fēng)除塵器的煙氣進(jìn)入布袋除塵器,煙氣從布袋除塵器下部孔板進(jìn)入圓筒形濾袋內(nèi),在通過(guò)濾料的孔隙時(shí),粉塵被捕集于濾料上,透過(guò)濾料的煙氣由排出口排出進(jìn)入脫硫程序。沉積在濾料上的粉塵,在機(jī)械振動(dòng)的作用下從濾料表面脫落,落入灰斗中,達(dá)到進(jìn)一步除塵的效果步驟三:將經(jīng)過(guò)脫硫工序的煙氣進(jìn)入是濕電除塵器。濕電除塵器采用采用高壓電暈針?lè)烹娛狗蹓m荷電,荷電的粒子在電場(chǎng)力的作用下到達(dá)集塵板,從而達(dá)到最佳除塵的效果,此時(shí)的煙氣已達(dá)到排放標(biāo)準(zhǔn),可以進(jìn)行排放。
28.②?
、熔分爐煙氣除塵:熔分爐產(chǎn)生的煙氣首先進(jìn)入旋風(fēng)除塵器進(jìn)行除塵后再進(jìn)入布袋除塵器進(jìn)行除塵,通過(guò)布袋除塵器的煙氣進(jìn)入脫硫塔進(jìn)行脫硫處理后的煙氣已達(dá)到排放標(biāo)準(zhǔn),可以進(jìn)行排放。(熔分爐旋風(fēng)除塵、布袋除塵的工序原理與還原爐旋風(fēng)除塵器、布袋除塵器工作原理相同)步驟(4)中的脫硫工藝為采用氣動(dòng)乳化脫硫工藝,其具體步驟為:采用工業(yè)純堿、石灰作為脫硫劑,把工業(yè)純堿、石灰制成脫硫液,將煙氣在脫硫液中充分接觸傳質(zhì),將煙氣中的二氧化硫和氟化物去除;脫硫后的煙氣經(jīng)除霧器除去細(xì)小液滴,然后排入有防腐層的濕煙囪,脫硫石膏漿經(jīng)脫水裝置脫水后運(yùn)出廠外處理。
29.脫硫:采用氣動(dòng)乳化脫硫工藝,采用工業(yè)純堿、石灰作為脫硫劑,其實(shí)質(zhì)為石灰-石膏濕法脫硫工藝,煙氣在塔內(nèi)與脫硫液充分接觸傳質(zhì),將煙氣中的so2和氟化物去除,同時(shí)可去除大部分煙塵。石灰-石膏濕法脫硫工藝采用工業(yè)純堿或者石灰做脫硫劑,工業(yè)純堿或者經(jīng)破碎磨細(xì)成粉狀的石灰與水混合攪拌成吸收漿液。目前濕法脫硫主要采用各種形式的空塔噴淋,在噴淋吸收塔內(nèi),吸收漿液與煙氣接觸混合,煙氣中二氧化硫與漿液中的碳酸鈣以及鼓入漿液的氧化空氣進(jìn)行化學(xué)反應(yīng)被脫除,最終反應(yīng)產(chǎn)物為石膏。脫硫后的煙氣經(jīng)除霧器除去細(xì)小液滴,然后排入有防腐層的濕煙囪。脫硫石膏漿經(jīng)脫水裝置脫水后運(yùn)出廠外處理石灰-石膏濕法脫硫工藝的主要化學(xué)反應(yīng)式如下:(1)吸收反應(yīng):so2+h2o
→
h2so3
→
hso3-+h+(2)溶解反應(yīng):ca(oh)2
→
ca2++2oh-;(3)氧化反應(yīng):hso3-+1/2o2
→
so42-+h+(4)結(jié)晶過(guò)程:ca2++so42-+2h2o
→
caso4
·
2h2o。
30.通過(guò)本技術(shù)方案,能夠從不銹鋼酸洗污泥中提取出高附加值的貴重金屬,從而有效實(shí)現(xiàn)其經(jīng)濟(jì)價(jià)值;并且本發(fā)明操作簡(jiǎn)單、而且生產(chǎn)成本較低,經(jīng)濟(jì)效果顯著,節(jié)約了成本的同時(shí)減少了環(huán)境的污染。
31.盡管已經(jīng)示出和描述了本發(fā)明的實(shí)施例,對(duì)于本領(lǐng)域的普通技術(shù)人員而言,可以理解在不脫離本發(fā)明的原理和精神的情況下可以對(duì)這些實(shí)施例進(jìn)行多種變化、修改、替換
和變型,本發(fā)明的范圍由所附權(quán)利要求及其等同物限定。技術(shù)特征:
1.一種不銹鋼酸洗污泥資源回收利用方法,其特征在于:其步驟為:(1)制球:將不銹鋼酸洗污泥、煉鋼除塵灰和煉鋼氧化鐵皮混合制成球狀體;(2)燒結(jié)預(yù)還原:將球狀體進(jìn)行烘干、燒結(jié)、預(yù)還原后形成基料;(3)熔分冶煉:將預(yù)還原后的基料送入熔分爐內(nèi)還原冶煉形成液態(tài)鎳鉻合金和爐渣,并通過(guò)渣鐵分離得到相互分離的鎳鉻合金和爐渣;(4)煙氣處理:基料在熔分爐內(nèi)熔分冶煉過(guò)程中進(jìn)行脫硝、脫硫、除塵工藝對(duì)煙氣進(jìn)行處理。2.根據(jù)權(quán)利要求1所述的一種不銹鋼酸洗污泥資源回收利用方法,其特征在于:步驟(1)的具體步驟為:將含水率 50 至 55%的不銹鋼酸洗污泥在混料場(chǎng)混入 6-8%的焦粉、 10%的煉鋼除塵灰、5%的煉鋼氧化鐵皮,將混合完成后的原料通過(guò)傳送帶輸送方式進(jìn)入制球機(jī),同時(shí)啟動(dòng)制球機(jī),制球機(jī)不斷旋轉(zhuǎn),經(jīng)過(guò)20-40 分鐘運(yùn)行,原料形成直徑為 3-5cm 的球狀固體,從制球機(jī)的出料口出料。3.根據(jù)權(quán)利要求1所述的一種不銹鋼酸洗污泥資源回收利用方法,其特征在于:步驟(2)的具體步驟包括:
①
進(jìn)料:將制球機(jī)制得的球狀固體經(jīng)皮帶輸送機(jī)輸送至還原爐爐頂后,自行滑落至旋轉(zhuǎn)布料器內(nèi),經(jīng)旋轉(zhuǎn)布料器在爐內(nèi)均勻布料;
②
烘干、燒結(jié)、預(yù)還原:首先在還原爐的干餾層利用爐內(nèi)高溫去除球狀固體中原料含有的水份,然后進(jìn)入爐膛后,原料中的焦炭粉和經(jīng)鼓風(fēng)機(jī)吹入爐膛內(nèi)的空氣進(jìn)行劇烈燃燒,散發(fā)熱量,使還原層的溫度達(dá)到800-1200度,原料中的鐵、鎳、鉻元素在高溫下預(yù)還原結(jié)晶,生成基料,
③
出料:預(yù)還原后的基料經(jīng)鼓風(fēng)機(jī)吹入常溫空氣進(jìn)行冷卻,當(dāng)基料溫度降至80-120度后,由旋轉(zhuǎn)出料器排出爐膛,通過(guò)出料皮帶輸送機(jī)運(yùn)送至基料中轉(zhuǎn)庫(kù);
④
還原燒結(jié)爐采用分批進(jìn)料方式,每20至30min進(jìn)一次料,一批料為4噸,出料采用連續(xù)出料方式,出料速度140至150千克/分鐘,燒結(jié)產(chǎn)生的基料通過(guò)皮帶機(jī)送入中轉(zhuǎn)庫(kù)。4.根據(jù)權(quán)利要求1所述的一種不銹鋼酸洗污泥資源回收利用方法,其特征在于:步驟(3)的具體步驟包括:
①
、進(jìn)料:將鎳鉻合金基料、焦碳、硅石按每個(gè)批次2000kg:300kg:30kg的比例配比混合均勻后,投入熔分爐電極周圍;
②
、熔分爐冶煉:對(duì)熔分爐內(nèi)進(jìn)行升溫,熔分爐內(nèi)高溫條件下,以碳作為還原劑對(duì)基料進(jìn)行還原反應(yīng)得到鎳鉻合金和爐渣;
③
、出料:熔分爐出鐵時(shí)間為4小時(shí)一次,鎳鉻合金與爐渣同時(shí)從出鐵口放出,即生產(chǎn)出fe含量40至60%左右,鎳含量4至8%、鉻含量12至18%左右的鎳鉻合金,爐渣通過(guò)位于熔分爐一端兩個(gè)排渣口之中的一個(gè)排渣口排渣,爐渣通過(guò)流槽進(jìn)入渣池,進(jìn)行水冷處理后進(jìn)行外運(yùn)送至水泥廠作為水泥生產(chǎn)原料。5.根據(jù)權(quán)利要求1所述的一種不銹鋼酸洗污泥資源回收利用方法,其特征在于:步驟(4)中的脫硝工藝為采用sncr脫硝工藝,其具體步驟為:將含有nhx基的還原劑與水混合后,還原劑稀釋為10%濃度的溶液,通過(guò)噴槍將稀釋后的溶液噴入爐膛內(nèi),使得稀釋后的溶液與煙氣進(jìn)行sncr反應(yīng)生成氮?dú)夂退?.根據(jù)權(quán)利要求1所述的一種不銹鋼酸洗污泥資源回收利用方法,其特征在于:步驟
(4)中的脫硫工藝為采用氣動(dòng)乳化脫硫工藝,其具體步驟為:采用工業(yè)純堿或者石灰作為脫硫劑,把工業(yè)純堿或石灰制成脫硫液,將煙氣在脫硫液中充分接觸傳質(zhì),將煙氣中的二氧化硫去除;脫硫后的煙氣經(jīng)除霧器除去細(xì)小液滴,然后排入有防腐層的濕煙囪,脫硫石膏漿經(jīng)脫水裝置脫水后運(yùn)出廠外處理。
技術(shù)總結(jié)
本發(fā)明涉及不銹鋼酸洗污泥回收技術(shù)領(lǐng)域,尤其是不銹鋼酸洗污泥資源回收利用方法,其步驟為:(1)制球:將不銹鋼酸洗污泥、煉鋼除塵灰和煉鋼氧化鐵皮混合制成球狀體;(2)燒結(jié)預(yù)還原:將球狀體進(jìn)行烘干、燒結(jié)、預(yù)還原后形成基料;(3)熔分冶煉:將預(yù)還原后的基料送入熔分爐內(nèi)還原冶煉形成液態(tài)鎳鉻合金和爐渣,并通過(guò)渣鐵分離得到相互分離的鎳鉻合金和爐渣;(4)煙氣處理:基料在熔分爐冶煉過(guò)程中進(jìn)行脫硝、脫硫、除塵工藝對(duì)煙氣進(jìn)行處理。本發(fā)明不僅會(huì)產(chǎn)生較大的效益并且會(huì)為環(huán)境保護(hù)和可持續(xù)發(fā)展做出巨大貢獻(xiàn)。做出巨大貢獻(xiàn)。做出巨大貢獻(xiàn)。
技術(shù)研發(fā)人員:沈繼程 鄒光遠(yuǎn) 周才華 鄒趙旭 李臻錕 葉煒
受保護(hù)的技術(shù)使用者:浙江瑞浦機(jī)械有限公司
技術(shù)研發(fā)日:2021.09.28
技術(shù)公布日:2022/2/7
聲明:
“不銹鋼酸洗污泥資源回收利用方法與流程” 該技術(shù)專利(論文)所有權(quán)利歸屬于技術(shù)(論文)所有人。僅供學(xué)習(xí)研究,如用于商業(yè)用途,請(qǐng)聯(lián)系該技術(shù)所有人。
我是此專利(論文)的發(fā)明人(作者)