難熔金屬鉭具有熔點高(2996℃,僅次于W和Re)、高溫強度高、熱膨脹系數(shù)低、導(dǎo)電性良好、可焊性能及極高的耐腐蝕性(常溫下可以與鉑媲美)等優(yōu)點[1~3],被廣泛應(yīng)用于電子電氣、化工、航空航天、醫(yī)療衛(wèi)生及軍事等領(lǐng)域,成為是高新技術(shù)領(lǐng)域中不可缺少的材料[4~10]。但鉭在地球中的儲量極少,僅為地殼質(zhì)量的0.0002%,因此,節(jié)約鉭資源的使用具有非常重要的意義。化學氣相沉積(CVD)是一種通過化學氣相反應(yīng)在被加熱的固體表面生成固態(tài)沉積物的工藝方法,具有沉積層純度高、致密、沉積速度快,可進行多元合金沉積等特點。由于CVD技術(shù)獨特的優(yōu)點,目前該技術(shù)已被廣泛的應(yīng)用于無機材料表面改性涂層制備、物質(zhì)提純、研制新晶體以及沉積各種單晶、玻璃態(tài)無機薄膜材料領(lǐng)域[10~13]。以CVD法在工件或容器內(nèi)壁上沉積一層鉭涂層,在保證材料具有良好的耐蝕性能的同時,可大大降低材料的使用量。CVD涂層的組織及性能強烈的依賴于其形核及生長條件,其影響因素主要有溫度、反應(yīng)氣體流量及比例、沉積壓力及反應(yīng)室形狀等。本實驗以冷壁式化學氣相沉積法在鉬基體上沉積鉭涂層,著重分析了氫氣流量對涂層沉積速率、組成、顯微組織及擇優(yōu)取向等的影響,為化學氣相沉積鉭的推廣應(yīng)用提供一定的參考依據(jù)。
1 實驗
化學氣相沉積鉭的原料為鉭片(純度>99.95%)、Cl2和H2,基體材料為采用粉末冶金加工態(tài)金屬鉬,尺寸為Ф28 mm×22 mm,每個基體表面均經(jīng)過相同處理以保證相同的表面狀態(tài)。
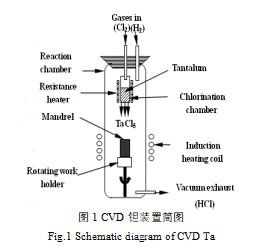
圖1為自制的CVD鉭氯化-還原聯(lián)合反應(yīng)裝置示意圖。沉積裝置由氯化室、沉積室、加熱系統(tǒng)、氣體輸運和真空系統(tǒng)組成。反應(yīng)氣體流量采用流量計控制,氯化加熱裝置采用電爐加熱,鉑銠熱電偶測量和調(diào)控加熱溫度,基體溫度采用可控硅感應(yīng)加熱,光學高溫計測溫。
表1所列為鉭涂層的沉積條件。
表1鉭涂層沉積條件
首先將整個系統(tǒng)抽真空,加熱基體和金屬原料鉭片到所需溫度,然后將經(jīng)凈化干燥處理的氯氣通入已被加熱到一定溫度裝有鉭片的氯化室中,氯氣與鉭在氯化室中發(fā)生反應(yīng)生成五氯化鉭。氣態(tài)五氯化鉭被輸運到已被感應(yīng)加熱到一定溫度的鉬基體表面,與氫氣發(fā)生還原反應(yīng)而沉積出鉭,基體旋轉(zhuǎn)以保證在沉積過程中產(chǎn)生均勻厚度的涂層。其主要化學反應(yīng)式為:
Ta+5/2Cl2=TaCl5 (1)
TaCl5+5H2= Ta+5HCl (2)
反應(yīng)所產(chǎn)生的廢氣經(jīng)過慮瓶捕集除塵后進入機械泵排出系統(tǒng)。
沉積樣品采用掃描電子顯微鏡(XL30 ESEM)進行形貌觀察。X-射線衍射儀進行物相分析(測試條件:Cu靶,40KV,80mA),并根據(jù)Harris公式計算織構(gòu)系數(shù)。用排水法(GB/T1 423-1996)測密度。顯微硬度計(HXS-1000A)測量硬度,加載為100g,加載時間為5s。每個樣品選取5個不同的點測硬度,取其平均值。
2實驗結(jié)果分析與討論
2.1 氫氣流量對沉積速率的影響
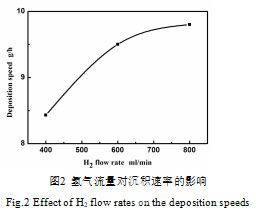
氫氣流量對沉積速率的影響如圖2所示,沉積速率隨氫氣流量增大而增加,超過600ml/min增速減緩。
沉積速率與氣體流量有強烈的依賴關(guān)系。在氣體流量較低時,反應(yīng)氣體在基體表面有足夠的停留時間參與反應(yīng),沉積速率受反應(yīng)氣體與固體表面上所發(fā)生反應(yīng)的附吸及解吸過程所控制,稱之為表面控制。反應(yīng)氣體流量的增加,在單位時間內(nèi)參與反應(yīng)的源物質(zhì)增加,使反應(yīng)向易于向生成物方向進行,使得沉積速率呈線性增加。反應(yīng)氣體流量繼續(xù)增大時,則會有部分氣體不起反應(yīng)直接從基體表面穿流而過,使反應(yīng)過程的效率降低。此時,沉積速率受反應(yīng)氣體的擴散及對流等物理過程所控制,稱之為質(zhì)量轉(zhuǎn)移控制。在這種情況下,沉積速率仍會隨反應(yīng)氣體流量的增大而增大,但不是呈線性關(guān)系,而是近似呈平方根的關(guān)系[13]。很顯然,由圖可知,氫氣流量對鉭涂層沉積速率的影響就是一個由表面控制向質(zhì)量轉(zhuǎn)移控制轉(zhuǎn)變的過程。
2.2 氫氣流量對涂層顯微組織及表面形貌的影響
沉積溫度保持不變時,氫氣流量對表面形貌的影響如圖3所示。隨氫氣流量的增大,涂層晶粒逐漸增大。采用線分法,又叫平均截線長度可法測量涂層晶粒尺寸。對同一樣品選取不同視場進行測量取其平均值,并計算晶粒度。計算方法如下[14]:
式中L平為平均截線長度,平均截線長度是指在截面上任意測試直線穿過每個晶粒長度的平均值。NL為單位測試線長度上截到的晶粒數(shù)目,LT為任意做的測試線的總長度,M為顯微鏡的放大倍數(shù),P為測試線與晶界的總交點數(shù),G為晶粒級別。測量結(jié)果見表2。
表2 氫氣與鉭涂層晶粒尺寸的關(guān)系
Table2. Relationship between H2 flow rate and grain size of Ta coatings
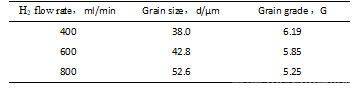
沉積溫度保持不變時,氫氣流量對表面形貌的影響如圖4所示。表面形貌呈現(xiàn)類金字塔狀顯微結(jié)構(gòu)。隨氫氣流量的增大,鉭的沉積速率加快,類金字塔狀的組織結(jié)構(gòu)的尺寸及高度相應(yīng)增加,從而導(dǎo)致整個沉積層的表面平整均勻度降低。
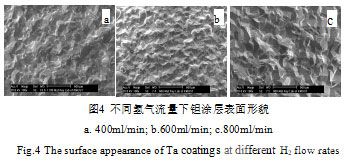
2.3 氫氣流量對涂層硬度的影響
表3 氫氣流量與硬度的關(guān)系
Table3 Relationship between H2 flow rates and micro-hardness H2 flow rate,ml/min Hardness,HV/×10Mpa
表2為不同氣體流量條件下CVD 鉭涂層的硬度。由表可知,隨著氣體流量的增加,硬度逐漸降低。由于沉積溫度不變,涂硬度的變化應(yīng)主要源于晶粒大小的變化。隨著氫氣流量增大,沉積層晶粒也相應(yīng)長大,從而導(dǎo)致細晶強化效果降低,硬度降低,與沉積溫度變化相比,氫氣流量對涂層硬度的影響要小得多[15]。
2.4 氫氣流量對涂層結(jié)構(gòu)的影響
對不同氫氣流量條件下的沉積樣品進行XRD分析,結(jié)果分別如圖5所示。由圖可知,各衍射峰位置與標準ASTM卡基本一致,無明顯偏移和寬化現(xiàn)象出現(xiàn),表明所獲得的鉭沉積層均由體心立方結(jié)構(gòu)的鉭(α-Ta)構(gòu)成。隨氫氣流量的變化,不同晶面衍射峰強度比值有所變化,則說明氫氣流量的變化對鉭涂層的晶粒擇優(yōu)取向有影響。
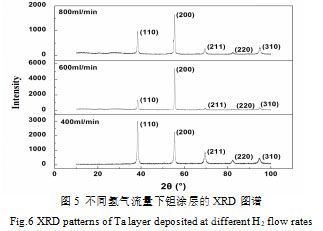
晶粒擇優(yōu)取向可用織構(gòu)系數(shù)TC(texture coefficient)來表征??棙?gòu)系數(shù)可由不同晶面強度比值及Harris公式計算得到[16]。圖7為氫氣流量對織構(gòu)系數(shù)的影響。可見當氫氣流量變化時,始終為{200}晶面方向織構(gòu)系數(shù)最大,即沉積層晶粒的擇優(yōu)取向主要受{200}晶面織構(gòu)系數(shù)影響。VAN DER DRIFT’S模型[17]認為:在最初的形核階段,晶粒隨機形核;接著,隨機形核的晶粒競爭生長;隨沉積時間增加,越來越多的晶粒被相鄰晶粒吞并,只剩下那些最快生長方向與基體表面垂直的晶粒,最終形成織構(gòu)。
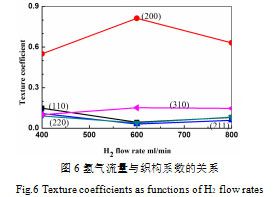
2.5 氫氣流量對涂層密度的影響
采用化學法將鉬基體去除后,可得到獨立的CVD鉭涂層,采用排水法對其進行密度測量,結(jié)果如表4所示。不同氫氣流量條件下所獲得的鉭涂層均具有較高的密度,涂層致密性好。隨氫氣流量的增加,鉭涂層密度逐漸升高,但變化幅度不大。
表4 氣體流量與密度的關(guān)系
3 結(jié)論
(1) 在本研究條件下,CVD鉭的沉積速率隨氫氣流量的增加而增大,晶粒尺寸在38.0~52.6μm之間,表面呈類金字塔狀顯微結(jié)構(gòu)。
(2) 涂層為體心立方結(jié)構(gòu)的鉭(α-Ta)構(gòu)成,沿(200)晶面方向生長最快。
(3) 涂層致密性好,相對密度在99.65%以上,維氏硬度在130.94~152.43之間。隨著反應(yīng)氣體流量的變化,沉積層密度及硬度的變化均不明顯。
聲明:
“氫氣流量對化學氣相沉積鉭涂層的影響” 該技術(shù)專利(論文)所有權(quán)利歸屬于技術(shù)(論文)所有人。僅供學習研究,如用于商業(yè)用途,請聯(lián)系該技術(shù)所有人。
我是此專利(論文)的發(fā)明人(作者)